Bearings play a critical role in the pulp and paper industry, ensuring the smooth and efficient operation of machinery and equipment. From wood preparation and pulping to paper production and finishing, bearings are essential components that support heavy loads, high speeds, and harsh operating conditions. The right choice of bearings can significantly enhance the reliability, performance, and lifespan of machinery, reducing downtime and maintenance costs. This guide provides an in-depth look at the various types of bearings used in the pulp and paper industry, their applications, and best practices for selection, maintenance, and troubleshooting to help optimize your operations and achieve superior results.
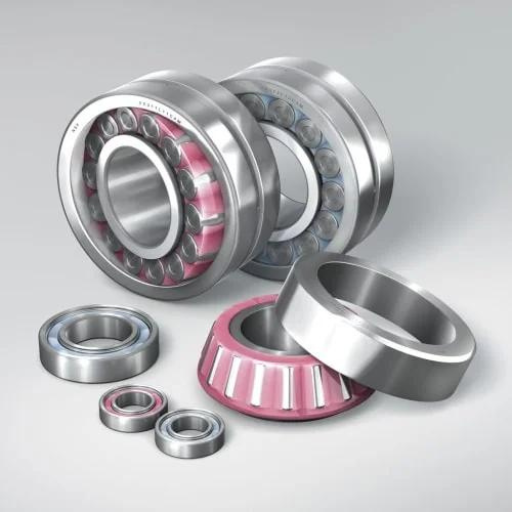
Pulp and Paper Industry Bearings
The pulp and paper industry relies on various types of bearings to maintain efficient and reliable operations across different stages of production. Each type of bearing is designed to meet specific demands and operational conditions, ensuring optimal performance and longevity. Here are the main bearing product classifications commonly used in the pulp and paper industry:
1. Ball Bearings
- Single Row Deep Groove Ball Bearings: Used for applications with moderate radial and axial loads.
- Angular Contact Ball Bearings: Ideal for applications requiring high-speed and high-precision operations.
2. Roller Bearings
- Cylindrical Roller Bearings: Known for high load-carrying capacity and low friction, suitable for heavy radial loads.
- Spherical Roller Bearings: Accommodate misalignment and are suitable for heavy radial and axial loads.
- Tapered Roller Bearings: Handle combined radial and axial loads and are commonly used in gearboxes and rolling mills.
3. Needle Bearings
- Needle Roller Bearings: Offer high load capacity with low cross-section, ideal for applications with limited space.
4. Thrust Bearings
- Thrust Ball Bearings: Handle axial loads in low-speed applications.
- Cylindrical Roller Thrust Bearings: Designed for high axial load applications, providing robust support and stability.
5. Plain Bearings
- Bushings and Sleeve Bearings: Provide reliable performance in low-speed, high-load applications with a simple design.
6. Specialty Bearings
- Hybrid Bearings: Utilize ceramic balls with steel races, offering high performance in harsh environments.
- Split Bearings: Simplify maintenance by allowing bearing replacement without disassembling surrounding equipment.
Each type of bearing has its specific advantages and is chosen based on the unique requirements of the application, including load capacity, speed, misalignment tolerance, and environmental conditions. Proper selection, installation, and maintenance of bearings are crucial for maximizing machinery uptime and minimizing operational costs in the pulp and paper industry.
Things to Note When Installing Bearings
Proper installation of bearings is crucial to ensure the longevity and optimal performance of machinery in the pulp and paper industry. Incorrect installation can lead to premature failure, increased maintenance costs, and unexpected downtime. Here are key points to consider during the installation process:
1. Preparation
- Clean Environment: Ensure the installation area is clean and free from dust and contaminants that can damage the bearing.
- Inspection: Check the bearing, housing, and shaft for any signs of damage or wear before installation.
- Tools: Use the correct tools and equipment for the installation process to prevent damage to the bearing and associated components.
2. Handling
- Proper Handling: Handle bearings with care to avoid any impacts or contamination. Use gloves to prevent corrosion from skin oils.
- Lubrication: Apply the appropriate type and amount of lubricant as specified by the manufacturer. Over-lubrication or under-lubrication can cause bearing failure.
3. Alignment
- Shaft and Housing Alignment: Ensure that the shaft and housing are properly aligned. Misalignment can lead to uneven load distribution and premature bearing wear.
- Correct Fit: Follow manufacturer guidelines for the correct fit between the bearing, shaft, and housing. Too tight or too loose fits can cause operational issues.
4. Mounting
- Temperature Control: Use appropriate methods such as heating or cooling to mount the bearing without applying excessive force. Induction heaters can be used to expand the bearing for easier installation.
- Uniform Pressure: Apply even pressure when mounting the bearing to avoid any misalignment or damage. Use bearing mounting sleeves or hydraulic nuts to ensure uniform pressure.
5. Securing the Bearing
- Locking Mechanism: Secure the bearing in place using the appropriate locking mechanism, such as set screws, lock nuts, or retaining rings, as recommended by the manufacturer.
- Axial Movement: Ensure that there is no unwanted axial movement after installation, which can affect the bearing’s performance.
6. Post-Installation Checks
- Rotation Check: After installation, rotate the bearing by hand to ensure it moves smoothly without any resistance or unusual noise.
- Load Application: Gradually apply the operational load to the bearing to ensure it is seated correctly and functioning as expected.
By following these guidelines, you can ensure that the bearings are installed correctly, leading to improved reliability, performance, and lifespan of the machinery in the pulp and paper industry.
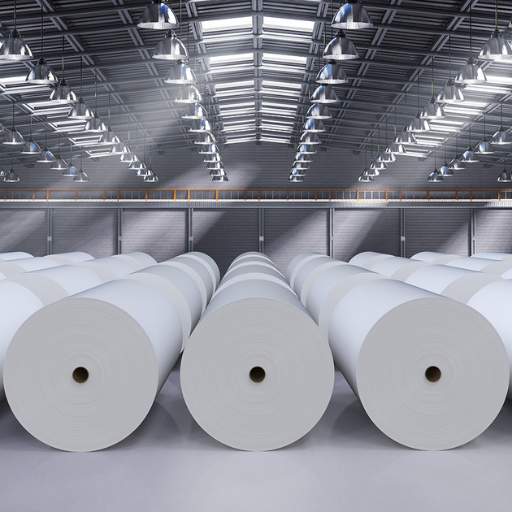
Problems That May Occur During Use of Bearings
Even with proper installation and maintenance, bearings in the pulp and paper industry can encounter various issues during operation. Identifying and addressing these problems promptly is essential to minimize downtime and prevent severe damage. Here are some common problems and their potential causes:
1. Excessive Bearing Temperature
- Causes:
- Over-lubrication or insufficient lubrication
- Incorrect type of lubricant
- Excessive load or speed beyond the bearing’s rating
- Misalignment of the bearing or shaft
- Solutions:
- Check and adjust lubrication levels and type
- Reduce load or operating speed
- Realign the bearing and associated components
2. Bearing Noise
- Causes:
- Contamination from dirt, dust, or debris
- Insufficient or degraded lubrication
- Bearing damage or wear
- Misalignment or looseness in the housing or shaft
- Solutions:
- Clean and lubricate the bearing
- Replace damaged bearings
- Ensure proper alignment and secure mounting
3. Vibration
- Causes:
- Misalignment of the bearing or shaft
- Imbalance in rotating components
- Loose bearing housing or fittings
- Bearing wear or damage
- Solutions:
- Check and correct alignment
- Balance rotating parts
- Tighten housing and fittings
- Replace worn or damaged bearings
4. Premature Bearing Wear
- Causes:
- Contamination from foreign particles
- Insufficient or improper lubrication
- Excessive loads or speeds
- Improper installation or handling
- Solutions:
- Ensure a clean operating environment
- Use the correct type and amount of lubricant
- Operate within the bearing’s load and speed ratings
- Follow proper installation procedures
5. Corrosion
- Causes:
- Exposure to moisture, chemicals, or corrosive environments
- Inadequate sealing or protection
- Solutions:
- Improve sealing and protection against contaminants
- Use corrosion-resistant bearings or coatings
- Regularly inspect and maintain the bearings
6. Fatigue Failure
- Causes:
- Repeated stress cycles beyond the bearing’s fatigue limit
- Inadequate lubrication
- Incorrect bearing selection for the application
- Solutions:
- Ensure proper lubrication and maintenance
- Select bearings appropriate for the load and operational conditions
- Regularly monitor and replace bearings as needed
7. Seizure
- Causes:
- Insufficient lubrication leading to metal-to-metal contact
- Overloading or excessive speed
- Contamination or debris causing obstruction
- Solutions:
- Ensure proper lubrication
- Reduce load or speed to within bearing specifications
- Keep the operating environment clean and free from contaminants
8. Electrical Erosion
- Causes:
- Electrical currents passing through the bearing, causing pitting or fluting
- Solutions:
- Use insulated bearings or grounding methods to prevent electrical currents from passing through the bearings
By understanding and addressing these common issues, you can maintain the efficiency and reliability of bearings in the pulp and paper industry, ensuring smooth and uninterrupted operations. Regular monitoring, maintenance, and adherence to best practices are key to mitigating these problems.
Product Clearance Requirements for Bearings
Proper clearance in bearings is essential for optimal performance and longevity, particularly in the demanding environments of the pulp and paper industry. Clearance refers to the total distance through which one bearing ring can be moved relative to the other, either radially (radial clearance) or axially (axial clearance). Here are the key factors to consider regarding bearing clearance requirements:
1. Radial Clearance
- Standard Radial Clearance: Most applications use standard radial clearance, which provides a balance between load capacity and operational smoothness.
- Increased Radial Clearance (C3, C4, etc.): Used in applications with high temperatures, heavy loads, or high speeds where thermal expansion or load-induced deformation might reduce clearance.
- Reduced Radial Clearance (C2): Suitable for high-precision applications with low temperatures and lighter loads where minimal clearance is needed.
2. Axial Clearance
- Standard Axial Clearance: Sufficient for most applications, ensuring that the bearing can handle axial loads without excessive movement or play.
- Custom Axial Clearance: May be required for specific applications where axial loads are significant, or precise axial positioning is crucial.
3. Temperature Considerations
- Thermal Expansion: High operating temperatures can cause bearing components to expand, reducing clearance. Bearings in high-temperature environments often need increased clearance to accommodate this expansion.
- Temperature Fluctuations: Applications with significant temperature changes may require special consideration of clearance to prevent bearing seizure or excessive play.
4. Load and Speed
- Heavy Loads: Bearings under heavy loads may deform slightly, reducing clearance. Increased radial clearance can help accommodate this deformation.
- High Speeds: High-speed applications often generate more heat, requiring bearings with increased clearance to prevent thermal expansion from causing contact between rolling elements and raceways.
5. Misalignment and Shaft Deflection
- Misalignment: Bearings designed to handle misalignment, such as spherical roller bearings, typically have more internal clearance to accommodate angular displacement.
- Shaft Deflection: Bearings used in applications with significant shaft deflection need sufficient clearance to prevent stress concentrations and potential bearing failure.
6. Lubrication
- Lubricant Type: The viscosity and type of lubricant can affect bearing clearance. Thicker lubricants may reduce clearance, while thinner lubricants may increase it.
- Lubrication Conditions: Bearings with increased clearance may be necessary in applications with boundary or mixed lubrication conditions to ensure adequate lubricant film formation.
Selecting the correct clearance for bearings is critical for ensuring optimal performance and longevity in the pulp and paper industry. It is essential to consult with bearing manufacturers and consider the specific operational conditions, including load, speed, temperature, and alignment, to determine the appropriate clearance for each application. Regular monitoring and adjustment of bearing clearance can further enhance machinery reliability and efficiency.
Product Sealing Requirements for Bearings
Sealing is a crucial aspect of bearing performance, especially in the pulp and paper industry where bearings are often exposed to harsh and contaminated environments. Proper sealing ensures the longevity and reliability of bearings by preventing contaminants from entering and retaining lubricants within the bearing. Here are key considerations for product sealing requirements:
1. Types of Seals
- Contact Seals (Lip Seals)
- Single Lip Seals: Provide basic protection against dust and light contaminants.
- Double Lip Seals: Offer enhanced protection against more severe contaminants and better lubricant retention.
- Non-Contact Seals (Shielded)
- Metal Shields: Effective in applications with minimal contamination; they offer less friction and heat generation.
- Labyrinth Seals: Provide high contamination protection without contact, suitable for high-speed applications.
2. Environmental Conditions
- Dust and Dirt: In environments with high levels of dust and dirt, robust sealing is essential to prevent abrasive particles from entering the bearing.
- Moisture and Water: Bearings exposed to moisture or water require seals that can prevent water ingress and protect against corrosion.
- Chemicals and Corrosives: Chemical exposure necessitates seals made from materials resistant to specific chemicals to ensure durability and protection.
3. Operating Conditions
- Temperature: High-temperature applications require seals made from materials that can withstand thermal expansion and maintain their integrity.
- Speed: High-speed applications benefit from non-contact seals that minimize friction and heat generation while providing adequate protection.
- Load: Heavy-load applications may need seals with enhanced durability to withstand the increased pressure and potential deformation.
4. Lubrication Retention
- Grease Lubrication: Seals should effectively retain grease within the bearing while preventing contaminants from mixing with the lubricant.
- Oil Lubrication: Seals must prevent oil leakage and ensure that the lubrication remains consistent throughout the bearing’s operation.
5. Seal Material
- Elastomers (Nitrile Rubber, Viton): Commonly used for their flexibility and resistance to a range of temperatures and chemicals.
- PTFE (Teflon): Offers excellent chemical resistance and can operate at higher temperatures.
- Metal: Provides mechanical protection and is often used in conjunction with other sealing materials for enhanced performance.
6. Application-Specific Sealing Solutions
- Pulping Equipment: Bearings in pulping equipment require seals that can handle the presence of wood particles, moisture, and chemicals used in the pulping process.
- Paper Machines: Bearings in paper machines are often exposed to water and chemicals used in the paper production process, necessitating robust sealing solutions to prevent ingress and maintain lubrication.
- Conveyors and Rollers: Bearings in conveyor systems and rollers need seals that can protect against dust and debris while ensuring smooth operation.
Selecting the appropriate sealing solution for bearings in the pulp and paper industry involves understanding the specific operational and environmental conditions. Proper sealing not only extends the life of the bearings but also ensures reliable and efficient operation of the machinery, reducing downtime and maintenance costs.
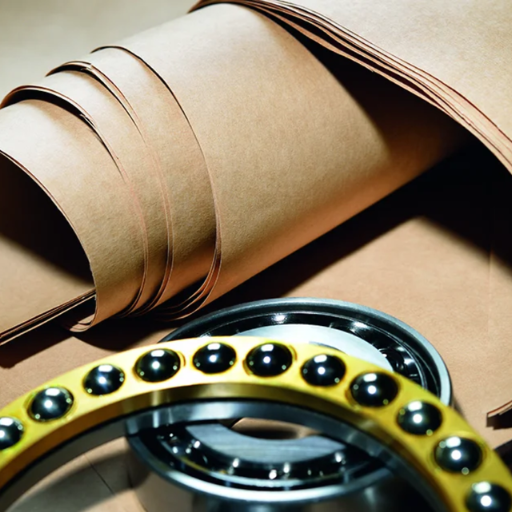
Usage Environment Requirements for Bearings in the Pulp and Paper Industry
Requirement |
Details |
Contaminant Exposure |
– Dust and Debris: Effective sealing to prevent contaminant entry. |
|
– Chemical Exposure: Resistance to acids, alkalis, and corrosive substances. |
|
– Moisture and Water: Seals to prevent water ingress and corrosion. |
Temperature Variations |
– High Temperatures: Bearings capable of withstanding heat without losing integrity or lubrication properties. |
|
– Low Temperatures: Bearings that maintain performance without becoming brittle or losing lubrication effectiveness. |
Load and Speed Requirements |
– High Loads: Bearings designed to handle heavy radial and axial loads. |
|
– High Speeds: Bearings that operate smoothly at high speeds without excessive heat generation or wear. |
Misalignment and Shaft Deflection |
– Accommodation of Misalignment: Bearings that handle misalignment and shaft deflection. |
|
– Flexibility: Use of flexible bearings like spherical roller bearings. |
Vibration and Shock Loads |
– Resistance to Vibration: Bearings that resist operational vibrations and imbalances. |
|
– Shock Load Capability: Bearings that withstand occasional shock loads without damage. |
Lubrication and Maintenance |
– Lubricant Compatibility: Bearings compatible with industry-specific lubricants. |
|
– Easy Maintenance: Bearings designed for easy maintenance and replacement. |
Corrosion Resistance |
– Corrosion-Resistant Materials: Bearings made from or coated with corrosion-resistant materials. |
|
– Protective Coatings: Use of protective coatings to enhance corrosion resistance. |
Environmental Regulations |
– Compliance with Standards: Bearings and lubricants that comply with environmental regulations and standards. |
Operational Reliability |
– Durability: Bearings that are durable and reliable under continuous operation. |
|
– Quality Assurance: High-quality bearings from reputable manufacturers for better performance and reliability. |
This table summarizes the key environmental requirements for bearings in the pulp and paper industry, providing a clear reference for selecting and maintaining bearings suited to these demanding conditions.
Temperature Requirements for Bearings
Temperature is a critical factor affecting the performance and longevity of bearings in the pulp and paper industry. Bearings must be able to operate effectively within a range of temperatures typically encountered in this sector. Here are the key considerations:
High Temperatures:
- Heat Resistance: Bearings must withstand high temperatures generated by machinery and processes without losing their structural integrity.
- Lubrication Stability: Lubricants used must retain their properties at high temperatures to ensure consistent bearing performance and minimize wear.
- Material Selection: Bearings may need to be made from or coated with materials that resist thermal degradation.
Low Temperatures:
- Cold Resistance: Bearings must maintain performance in low-temperature conditions without becoming brittle.
- Lubrication Effectiveness: Lubricants must be effective at low temperatures to prevent increased friction and wear.
Temperature Fluctuations:
- Thermal Expansion: Bearings should accommodate thermal expansion and contraction to avoid issues with clearance and alignment.
- Consistent Performance: Bearings must provide reliable performance despite temperature variations to ensure uninterrupted operation.
By addressing these temperature-related requirements, bearings in the pulp and paper industry can achieve optimal performance, reliability, and longevity, contributing to the overall efficiency of the machinery and processes.
Lubricant Selection for Bearings
Choosing the right lubricant for bearings in the pulp and paper industry is crucial for ensuring optimal performance, reliability, and longevity. Lubricants play a vital role in reducing friction, preventing wear, and protecting against corrosion. Here are the key considerations for selecting the appropriate lubricant:
1. Types of Lubricants
- Grease: Commonly used for its ability to stay in place and provide long-lasting lubrication.
- Lithium-Based Grease: Suitable for general applications with moderate temperatures and loads.
- Calcium-Based Grease: Provides good water resistance, ideal for wet environments.
- Polyurea Grease: Excellent for high-temperature applications.
- Oil: Used in applications requiring efficient heat dissipation and high-speed operation.
- Mineral Oils: Suitable for general-purpose lubrication.
- Synthetic Oils: Offer better performance in extreme temperatures and high-load conditions.
2. Temperature Range
- High-Temperature Stability: Lubricants must maintain their viscosity and lubricating properties at high temperatures to prevent bearing failure.
- Low-Temperature Performance: Lubricants should not thicken excessively at low temperatures, which can impede bearing movement.
3. Load Carrying Capacity
- Extreme Pressure (EP) Additives: Lubricants with EP additives are essential for bearings subjected to high loads, as they provide additional protection against metal-to-metal contact.
- Anti-Wear Additives: Help reduce wear and extend bearing life under heavy load conditions.
4. Water Resistance
- Hydrophobic Properties: Lubricants with strong water-resistant properties are necessary to protect bearings from moisture and water ingress, particularly in wet sections of the pulp and paper process.
5. Corrosion Protection
- Rust Inhibitors: Lubricants containing rust inhibitors protect bearings from corrosion caused by exposure to moisture and chemicals.
6. Contamination Resistance
- Seal Compatibility: Ensure the lubricant is compatible with the bearing seals to maintain effective sealing and prevent contamination ingress.
- Filterability: For oil-lubricated systems, the lubricant should be easily filterable to remove contaminants and extend its service life.
7. Application-Specific Considerations
- Pulping Equipment: Requires lubricants that can withstand high loads, moisture, and contaminants.
- Paper Machines: Needs lubricants that perform well under high-speed and high-temperature conditions.
- Conveyors and Rollers: Benefit from lubricants with good water resistance and load-carrying capacity.
8. Maintenance and Replenishment
- Lubrication Intervals: Select lubricants that provide long service intervals to reduce maintenance frequency and operational downtime.
- Re-Lubrication Systems: For critical applications, consider automatic re-lubrication systems to ensure consistent lubrication and reduce the risk of bearing failure.
By considering these factors, you can select the most suitable lubricant for bearings in the pulp and paper industry, ensuring enhanced performance, reliability, and service life of the equipment.
Selection of Bearing Type for the Pulp and Paper Industry
Choosing the right type of bearing for the pulp and paper industry is essential to ensure reliable operation, minimize downtime, and extend the lifespan of machinery. Here are the main considerations and common types of bearings used in this industry:
1. Operational Conditions
- Load Type: Determine whether the bearing will primarily experience radial, axial, or combined loads.
- Speed: Assess the operational speed of the machinery, as different bearings are suited to different speed ranges.
- Temperature: Consider the operational temperature range to select bearings that can withstand these conditions.
- Misalignment: Evaluate the potential for misalignment in the application to choose bearings that can accommodate it.
2. Bearing Types
Ball Bearings
- Single Row Deep Groove Ball Bearings: Suitable for moderate radial and axial loads, high-speed applications.
- Applications: Electric motors, conveyor rollers.
- Angular Contact Ball Bearings: Designed for high-speed and high-precision applications, handling combined loads.
- Applications: Precision machinery, pumps.
Roller Bearings
- Cylindrical Roller Bearings: High radial load capacity, low friction, suitable for heavy loads.
- Applications: Gearboxes, rolling mills.
- Spherical Roller Bearings: Accommodate misalignment, suitable for heavy radial and axial loads.
- Applications: Pulping equipment, vibrating screens.
- Tapered Roller Bearings: Handle combined radial and axial loads, commonly used in gearboxes and heavy-duty machinery.
- Applications: Rolling mills, conveyors.
Needle Bearings
- Needle Roller Bearings: High load capacity with low cross-section, ideal for limited space applications.
- Applications: Printing presses, material handling equipment.
Thrust Bearings
- Thrust Ball Bearings: Designed to handle axial loads in low-speed applications.
- Applications: Low-speed machinery, auxiliary equipment.
- Cylindrical Roller Thrust Bearings: High axial load capacity, providing robust support and stability.
- Applications: Industrial presses, vertical shaft applications.
Plain Bearings
- Bushings and Sleeve Bearings: Simple design, reliable performance in low-speed, high-load applications.
- Applications: Pulp and paper machines, drying cylinders.
Specialty Bearings
- Hybrid Bearings: Utilize ceramic balls with steel races, offering high performance in harsh environments.
- Applications: High-speed applications, chemically aggressive environments.
- Split Bearings: Simplify maintenance by allowing bearing replacement without disassembling surrounding equipment.
- Applications: Difficult-to-access machinery, critical equipment requiring minimal downtime.
3. Application-Specific Requirements
- Pulping Equipment: Bearings must handle heavy loads, contaminants, and moisture. Spherical roller bearings are often preferred for their load capacity and alignment tolerance.
- Paper Machines: Bearings must perform well at high speeds and temperatures. Cylindrical roller bearings and deep groove ball bearings are commonly used.
- Conveyors and Rollers: Require bearings that resist dust, debris, and moisture. Sealed deep groove ball bearings and spherical roller bearings are suitable.
By carefully considering these factors, you can select the most appropriate bearing type for each application within the pulp and paper industry, ensuring optimal performance and longevity of your equipment. Regular maintenance and monitoring are also essential to maximize the lifespan and efficiency of the selected bearings.

Bearing Life in the Pulp and Paper Industry
Bearing life is a critical factor in the performance and reliability of machinery in the pulp and paper industry. Proper understanding and management of bearing life can significantly reduce downtime, maintenance costs, and overall operational disruptions. Here’s a detailed overview of bearing life, its influencing factors, and how to maximize it:
1. Definition of Bearing Life
- Basic Rating Life (L10 Life): The number of revolutions or hours at a given speed that 90% of a group of identical bearings will achieve or exceed before showing signs of fatigue.
- Average Life (L50 Life): The median life expectancy of a bearing, indicating the point at which 50% of the bearings will have failed due to fatigue.
2. Factors Influencing Bearing Life
Load
- Radial and Axial Loads: Higher loads, both radial and axial, reduce bearing life. Ensure bearings are rated for the specific load conditions of the application.
- Shock Loads: Sudden, unexpected loads can cause premature bearing failure. Bearings in applications with shock loads should have higher load ratings or protective features.
Speed
- Operating Speed: Bearings have speed limits. Operating above the rated speed increases temperature and wear, reducing bearing life.
- Speed Variability: Fluctuations in speed can impact bearing performance and longevity.
Lubrication
- Type and Quality of Lubricant: Using the correct lubricant and maintaining its quality is crucial. Inadequate or contaminated lubrication leads to increased friction and wear.
- Lubrication Interval: Regular re-lubrication according to manufacturer specifications ensures consistent performance and extends bearing life.
Temperature
- Operating Temperature: High temperatures accelerate lubricant degradation and material fatigue, shortening bearing life.
- Thermal Expansion: Significant temperature changes can cause differential expansion in bearing components, affecting clearance and performance.
Contamination
- Environmental Contaminants: Dust, dirt, moisture, and chemicals can enter the bearing, causing wear and corrosion. Effective seals and proper housing design help mitigate this.
- Internal Contaminants: Metal particles from wear or improper lubrication can damage bearing surfaces.
Alignment and Installation
- Misalignment: Bearings must be properly aligned to avoid uneven load distribution, which can lead to premature failure.
- Installation Practices: Incorrect installation techniques, such as using excessive force or improper tools, can damage bearings.
Basic Dynamic Load Rating and Fatigue Life in Bearings
Basic Dynamic Load Rating (C)
The Basic Dynamic Load Rating (C) is a fundamental parameter used to describe the load-carrying capacity of a bearing. It is defined as the constant load that a bearing can theoretically endure for a basic rating life of one million revolutions. This rating is provided by the bearing manufacturer and is a critical factor in determining the appropriate bearing for a given application.
- Definition: The load that the bearing can sustain for a rating life of one million revolutions.
- Purpose: To provide a standardized measure for comparing the load-carrying capabilities of different bearings.
- Units: Typically expressed in Newtons (N) or pounds-force (lbf).
The Basic Dynamic Load Rating helps engineers select the correct bearing based on the expected operational loads and desired lifespan.
Fatigue Life (L10 Life)
Fatigue life, often referred to as L10 life, is the expected lifespan of a bearing under specific operating conditions. It represents the number of revolutions or hours at a given speed that 90% of a group of identical bearings will achieve or exceed before showing signs of fatigue failure.
- Definition: The number of revolutions or hours that 90% of a group of bearings will achieve without fatigue failure.
- Calculation: Based on the dynamic load rating and the actual operating load.
- Expression: Typically given in millions of revolutions (L10) or hours of operation (L10h).
Dynamic Equivalent Load (P)
The Dynamic Equivalent Load (P) is a calculated load value that represents the combined effect of both radial and axial loads acting on a bearing. This load is used in bearing life calculations to provide a simplified yet accurate representation of the actual operating conditions that the bearing experiences. It is essential for determining the fatigue life of the bearing using the Basic Dynamic Load Rating (C).
Definition
The Dynamic Equivalent Load (P) is the hypothetical load, constant in magnitude and direction, that if applied to a bearing would have the same effect on the bearing’s life as the actual loads to which the bearing is subjected.
Basic Static Load Ratings and Static Equivalent Loads
Basic Static Load Rating (C₀)
The Basic Static Load Rating (C₀) is a critical parameter for bearings that represents the maximum static load that a bearing can withstand without experiencing permanent deformation of the bearing components. This rating is essential for applications where bearings are subjected to heavy loads while stationary or experiencing very slow movements.
- Definition: The load that causes a defined permanent deformation at the contact points between the rolling elements and the raceways.
- Purpose: To provide a measure of the bearing’s capacity to handle heavy loads without suffering permanent damage.
- Units: Typically expressed in Newtons (N) or pounds-force (lbf).
The static load rating is crucial for ensuring that bearings do not suffer from brinelling (indentation) under heavy loads, which can lead to increased noise, vibration, and reduced bearing life.
Static Equivalent Load (P₀)
The Static Equivalent Load (P₀) is a hypothetical load that, if applied to the bearing, would cause the same amount of deformation as the actual loads acting on the bearing. It is used to compare the actual loading conditions to the bearing’s static load rating.
- Definition: A simplified load that represents the combined effect of the actual radial and axial loads acting on a bearing.
- Calculation: Similar to the dynamic equivalent load, the static equivalent load is calculated based on the actual radial and axial loads and specific factors for different types of bearings.
Bearing Tolerances
Bearing tolerances are critical parameters that define the permissible limits of deviation for the dimensions and performance characteristics of a bearing. These tolerances ensure that bearings fit and function correctly within their applications, maintaining the necessary precision and performance. Understanding bearing tolerances is essential for selecting the right bearing for a given application and ensuring its reliable operation.
Types of Bearing Tolerances
Dimensional Tolerances
- Bore Diameter (d)
- Outer Diameter (D)
- Width (B)
- Chamfer Dimensions
- Inner Ring Width (C)
Running Accuracy Tolerances
- Radial Runout: The deviation in the radial distance between the bearing’s inner and outer rings.
- Axial Runout: The deviation in the axial distance between the bearing’s inner and outer rings.
- Face Runout with Bore and O.D.
- Raceway Width Variation
Tolerance Classes
Bearings are manufactured to different tolerance classes, which define the permissible deviations for their dimensions and running accuracy. The most commonly used tolerance classes are set by international standards such as ISO, ANSI/ABMA, and JIS.
ISO Tolerance Classes:
Normal (PN): Standard tolerance suitable for most general applications.
Class 6 (P6): Higher precision for applications requiring better alignment and accuracy.
Class 5 (P5): Even higher precision for demanding applications such as high-speed machinery.
Class 4 (P4): Ultra-precision for critical applications like precision instruments and aerospace.
Class 2 (P2): Highest precision for extremely demanding applications.
ANSI/ABMA and JIS Standards: Similar classification with slight variations in the designation.
Fits and Internal Clearances for Bearings
Proper fits and internal clearances are crucial for the optimal performance and longevity of bearings in various applications, including the pulp and paper industry. These factors ensure that the bearings operate smoothly, handle loads efficiently, and minimize wear and tear.
Fits
- Bearing Fits:Bearing fits refer to the dimensional relationship between the bearing’s inner ring and the shaft, as well as the outer ring and the housing. The correct fit prevents slippage and ensures the bearing can carry the load effectively.
Types of Fits:
- Interference Fit (Press Fit):The bearing ring is slightly larger than the shaft or housing, requiring force to assemble. This fit is typically used for applications with high loads and low speeds.
- Transition Fit:A compromise between interference and clearance fits, providing a slight overlap. Suitable for applications where slight movement is acceptable.
- Clearance Fit:The bearing ring is slightly smaller than the shaft or housing, allowing for easy assembly and disassembly. Ideal for applications with low loads and high speeds.
Fit Selection:
- Shaft Fits:
- Loose Fit (H6/g6, H7/h6):Allows easy assembly and disassembly. Used for applications with low loads and high speeds.
- Transition Fit (H7/k6, H7/m6):Provides a balance between security and ease of assembly. Suitable for medium loads and speeds.
- Interference Fit (H7/n6, H7/p6):Ensures a secure fit for high loads and low speeds. Requires careful assembly techniques.
- Housing Fits:
- Loose Fit (H7/g7):Used for outer rings with low loads and high speeds.
- Transition Fit (H7/k7):Suitable for applications with medium loads.
- Interference Fit (H7/n7):Provides a secure fit for high-load applications.
Fit Recommendations (ISO 286-2 Standard):
Shaft Dia. Range (mm) |
Loose Fit (g6) |
Transition Fit (k6) |
Interference Fit (n6) |
10 – 18 |
+10 to +22 |
+4 to +17 |
-2 to +11 |
18 – 30 |
+12 to +25 |
+5 to +20 |
-3 to +14 |
30 – 50 |
+15 to +30 |
+6 to +24 |
-4 to +17 |
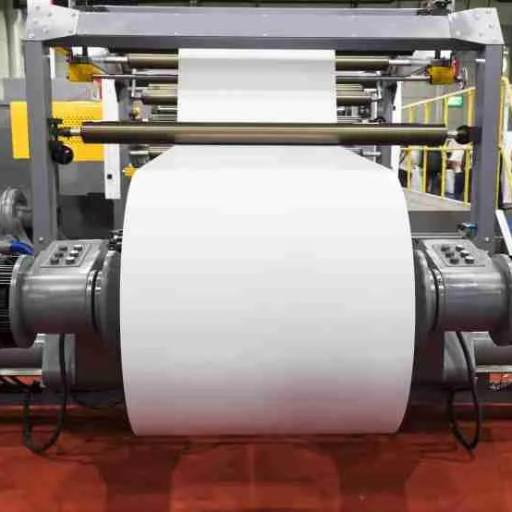
Lubrication of Bearings in the Pulp and Paper Industry
Proper lubrication is essential for the performance and longevity of bearings, especially in the demanding environments of the pulp and paper industry. Lubrication reduces friction, prevents wear, protects against corrosion, and helps dissipate heat. Here are the key considerations for bearing lubrication:
Types of Lubricants
- Grease:
- Composition:Typically consists of a base oil, thickener, and additives.
- Advantages:Stays in place, provides a sealing effect, and requires less frequent re-application.
- Common Types:
- Lithium-Based Grease:Suitable for general applications.
- Calcium-Based Grease:Offers good water resistance.
- Polyurea Grease:Excellent for high-temperature applications.
- Synthetic Grease:Suitable for extreme conditions, providing superior performance in both high and low temperatures.
- Oil:
- Composition:Base oil with additives.
- Advantages:Better heat dissipation, suitable for high-speed applications, and can be filtered to remove contaminants.
- Common Types:
- Mineral Oil:Suitable for general-purpose lubrication.
- Synthetic Oil:Provides better performance in extreme temperatures and high-load conditions.
- Biodegradable Oil:Environmentally friendly option for applications with environmental regulations.
Lubrication Methods
- Manual Lubrication:
- Method:Applying lubricant by hand or using a grease gun.
- Frequency:Depends on the application, load, speed, and environmental conditions.
- Automatic Lubrication Systems:
- Method:Automated systems deliver the right amount of lubricant at specified intervals.
- Advantages:Ensures consistent lubrication, reduces maintenance intervals, and minimizes the risk of under- or over-lubrication.
- Centralized Lubrication Systems:
- Method:A centralized system distributes lubricant to multiple bearings from a single location.
- Advantages:Efficient for large installations with numerous bearings, reducing maintenance time and ensuring consistent lubrication.
Factors Influencing Lubrication Choice
- Load and Speed:
- High loads require lubricants with extreme pressure (EP) additives.
- High speeds need lubricants with good thermal stability and low viscosity.
- Temperature:
- High temperatures require lubricants with high thermal stability and low volatility.
- Low temperatures need lubricants that remain fluid and effective.
- Environmental Conditions:
- Moist environments necessitate lubricants with strong water resistance.
- Dusty or dirty environments require lubricants with good sealing properties to prevent contamination ingress.
- Bearing Type and Application:
- Roller bearings typically need different lubrication than ball bearings due to their load and speed characteristics.
- Specific applications, like paper machines, may have unique lubrication needs based on operational demands.
Lubrication Practices
- Proper Application:
- Apply the right amount of lubricant to prevent overheating (from too much) or increased wear (from too little).
- Regular Maintenance:
- Check and replenish lubricants as needed based on manufacturer recommendations and operating conditions.
- Monitoring Lubricant Condition:
- Regularly test the lubricant for contamination, viscosity changes, and degradation to ensure it remains effective.
By carefully selecting and applying the appropriate lubricants, and following best practices for lubrication, the performance and lifespan of bearings in the pulp and paper industry can be significantly enhanced, leading to reduced maintenance costs and increased machinery reliability.
Materials for Bearing Rings and Rolling Elements
The materials used for bearing rings and rolling elements are critical to the performance, durability, and reliability of bearings. These materials must withstand various stresses, loads, and environmental conditions commonly encountered in the pulp and paper industry, among other sectors. Below are the most common materials used for bearing rings and rolling elements:
1. Steel
Steel is the most widely used material for bearing rings and rolling elements due to its excellent properties, including strength, hardness, and fatigue resistance.
Types of Steel:
High-Carbon Chrome Steel (SAE 52100, AISI 52100, GCr15):
-
- Properties:High hardness, excellent wear resistance, and good fatigue strength.
- Applications:Standard bearing rings and rolling elements for a wide range of applications.
Through-Hardened Steel:
-
- Properties:Uniform hardness throughout the material, suitable for high-load and high-speed applications.
- Applications:General-purpose bearings, including ball and roller bearings.
Case-Hardened Steel (Case-Carburized Steel):
-
- Properties:Hard surface layer with a tough, ductile core, providing excellent impact resistance and toughness.
- Applications:Heavy-duty applications where shock loads are common.
Stainless Steel (AISI 440C, AISI 304, AISI 316):
-
- Properties:Corrosion-resistant, suitable for harsh environments.
- Applications:Bearings in corrosive environments, food processing, and medical equipment.
2. Ceramics
Ceramics offer exceptional properties for specialized applications, particularly where high temperatures, corrosion, and low friction are concerns.
Types of Ceramics:
Silicon Nitride (Si3N4):
-
- Properties:High hardness, low density, high temperature resistance, and excellent corrosion resistance.
- Applications:High-speed bearings, high-temperature applications, and vacuum environments.
Zirconia (ZrO2):
-
- Properties:High fracture toughness and resistance to wear.
- Applications:Specialty bearings, including those in corrosive and high-temperature environments.
3. Hybrid Bearings
Hybrid bearings combine steel rings with ceramic rolling elements to leverage the advantages of both materials.
Advantages:
- Reduced Weight:Ceramic rolling elements are lighter than steel, reducing the overall weight of the bearing.
- Lower Friction:Ceramics have lower friction, improving efficiency and reducing heat generation.
- Higher Speed Capability:Hybrid bearings can operate at higher speeds due to the reduced weight and friction.
- Corrosion Resistance:Ceramics are resistant to corrosion, enhancing the bearing’s performance in harsh environments.
Introduction to Major Bearing Brands
There are several renowned brands in the bearing industry, each offering unique products and technologies that cater to various applications. Understanding the differences between these brands can help in selecting the most suitable bearings for specific needs. Below is an overview of some major bearing brands, highlighting their strengths and specializations.
1. SKF (Swedish Company)
- Overview: SKF is one of the largest and most well-known bearing manufacturers globally, offering a comprehensive range of products and services.
- Strengths:
- Innovation: Strong focus on research and development, leading to advanced bearing technologies.
- Quality: High standards of manufacturing and quality control.
- Service: Extensive global service network providing support and maintenance solutions.
- Special Products:
- Explorer Series: Enhanced performance and longer life due to improved material and manufacturing techniques.
- E2 Series: Energy-efficient bearings designed to reduce friction and energy consumption.
2. NSK (Japanese Company)
- Overview: NSK is a leading Japanese bearing manufacturer known for its high-quality products and innovative solutions.
- Strengths:
- Precision: Excellent manufacturing precision, suitable for high-speed and high-precision applications.
- Diverse Range: Wide variety of bearings catering to different industries.
- Research: Strong emphasis on research and development.
- Special Products:
- HPS Series: High-performance standard bearings offering superior load capacity and extended life.
- Spacea Series: Bearings designed for extreme environments, such as vacuum, high temperature, and corrosive conditions.
3. FAG (German Company) – Part of Schaeffler Group
- Overview: FAG, now part of the Schaeffler Group, is a prominent German bearing brand with a rich history of innovation and quality.
- Strengths:
- Technology: Advanced bearing technology and precision engineering.
- Reliability: Known for producing robust and reliable bearings.
- Application-Specific Solutions: Tailored solutions for various industries.
- Special Products:
- X-life Bearings: Enhanced performance bearings with higher load-carrying capacity and longer service life.
- Sensor Bearings: Bearings integrated with sensors for monitoring conditions like speed, temperature, and load.
4. Timken (American Company)
- Overview: Timken is a leading American manufacturer specializing in tapered roller bearings and power transmission products.
- Strengths:
- Tapered Roller Bearings: Expertise in producing high-quality tapered roller bearings.
- Durability: Bearings designed for heavy-duty applications with high durability.
- Innovation: Focus on developing innovative bearing solutions.
- Special Products:
- Timken MileMate®: Pre-adjusted wheel bearing assemblies for trucks and trailers.
- Corrosion-Resistant Bearings: Bearings designed for harsh environments with enhanced corrosion resistance.
5. NTN (Japanese Company)
- Overview: NTN is another major Japanese bearing manufacturer, offering a wide range of products for various industries.
- Strengths:
- Quality Control: Stringent quality control measures ensuring high reliability.
- Global Presence: Extensive global network providing local support.
- Innovation: Continuous development of new technologies and products.
- Special Products:
- Topline Series: Bearings designed for extreme conditions such as high-speed, high-temperature, and corrosive environments.
- Sentinel Series: Maintenance-free bearings with solid lubrication for food and beverage applications.
6. INA (German Company) – Part of Schaeffler Group
- Overview: INA, also part of the Schaeffler Group, specializes in needle bearings and linear motion products.
- Strengths:
- Needle Bearings: Expertise in producing high-quality needle bearings.
- Linear Motion: Comprehensive range of linear motion products.
- Engineering Support: Strong focus on providing engineering support and customized solutions.
- Special Products:
- MachLine Bearings: Precision bearings for machine tools and automation.
- Track Roller Guidance Systems: Advanced linear guidance systems for various industrial applications.
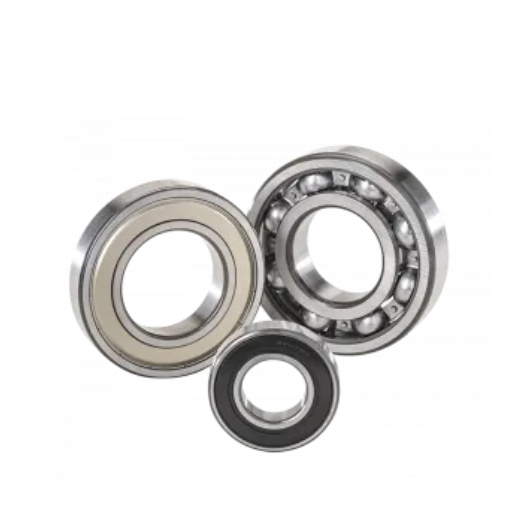
Application of Major Bearing Brands in the Pulp and Paper Industry
The pulp and paper industry requires robust, reliable, and efficient bearings to handle the harsh operating conditions, heavy loads, high speeds, and continuous operation typical of this sector. Below is an overview of how major bearing brands cater to the specific needs of the pulp and paper industry:
1. SKF (Swedish Company)
- Applications:
- Wood Preparation: SKF bearings are used in chippers, debarkers, and conveyors, providing high load capacity and durability.
- Pulping: Bearings in pulpers, refiners, and agitators must withstand heavy loads and contaminants. SKF’s sealed bearings and maintenance-free solutions are ideal here.
- Paper Machines: High-speed bearings for dryers, calendars, and rolls, utilizing SKF’s Explorer series for enhanced performance and longevity.
- Finishing: Bearings for cutters, winders, and rewinders, offering precision and reliability.
- Advantages: Innovative technologies, extensive service network, energy-efficient solutions.
2. NSK (Japanese Company)
- Applications:
- Stock Preparation: Bearings for screens, refiners, and pumps, providing high precision and reliability.
- Forming Section: High-speed bearings for forming rolls and couch rolls, using NSK’s high-performance HPS series.
- Press Section: Bearings that can handle high loads and moisture, ensuring long life and low maintenance.
- Dryer Section: High-temperature bearings with excellent heat resistance for dryer cylinders.
- Advantages: High precision, innovative materials, strong focus on R&D.
3. FAG (German Company) – Part of Schaeffler Group
- Applications:
- Chippers and Debarkers: Bearings that can handle shock loads and harsh environments.
- Pulping Equipment: Robust bearings for pulpers and refiners, ensuring reliability under heavy loads.
- Paper Machines: X-life bearings for press rolls and dryer sections, offering extended service life and higher load capacity.
- Finishing Equipment: Precision bearings for winders and cutters, providing smooth operation and long life.
- Advantages: Advanced technology, high reliability, application-specific solutions.
4. Timken (American Company)
- Applications:
- Wood Handling: Tapered roller bearings for chippers and conveyors, providing durability and high load capacity.
- Pulping Processes: Bearings for mixers and agitators, ensuring resistance to contamination and high loads.
- Press and Dryer Sections: High-performance bearings that handle high speeds and temperatures.
- Finishing Operations: Bearings for slitting and rewinding machines, ensuring precision and reliability.
- Advantages: Expertise in tapered roller bearings, durable solutions for heavy-duty applications.
5. NTN (Japanese Company)
- Applications:
- Conveyors and Rollers: Durable bearings for material handling and conveyor systems.
- Pulping Equipment: Bearings that resist contamination and provide long service life under heavy loads.
- Forming and Press Sections: High-speed, high-load bearings for critical sections of the paper machine.
- Drying and Finishing: High-temperature and corrosion-resistant bearings for dryers and finishers.
- Advantages: High-quality control, global support network, innovative solutions.
6. INA (German Company) – Part of Schaeffler Group
- Applications:
- Needle Bearings: Suitable for applications with limited space and high loads, such as various auxiliary equipment.
- Linear Motion: Bearings for precise linear movement in cutting and finishing machines.
- Pulping and Refining: Robust bearings that handle heavy loads and resist contamination.
- Paper Machines: High-precision bearings for critical sections, ensuring smooth operation and long service life.
- Advantages: Expertise in needle bearings and linear motion, strong engineering support.
Interchangeability of Bearing Types Between Different Brands
Bearing interchangeability refers to the ability to replace a bearing from one brand with a bearing from another brand without significant changes in fit, function, or performance. This is particularly useful for maintenance and replacement in industries like pulp and paper, where minimizing downtime is crucial.
Key Considerations for Bearing Interchangeability
Dimensional Compatibility:
- Ensure that the critical dimensions (bore diameter, outer diameter, width) of the bearings are identical.
- Check for compatibility in terms of tolerances and fits.
Load and Speed Ratings:
- Compare the dynamic and static load ratings of the bearings.
- Ensure that the speed ratings match the application requirements.
Internal Clearance:
- Verify that the internal clearance (C2, CN, C3, etc.) is appropriate for the application and matches the original bearing.
Material and Quality:
- Ensure that the materials used in the bearings (steel type, heat treatment, coatings) are suitable for the application.
- Verify that the replacement bearing meets or exceeds the quality and performance standards of the original.
Seals and Shields:
- If the original bearing has specific seals or shields, ensure the replacement bearing has equivalent sealing solutions to protect against contamination.
Application-Specific Features:
- Check for any special features (e.g., low-noise, high-temperature, corrosion-resistant) that may be required for the application.
Common Bearing Interchange Guides
1. SKF
- Interchange Guides: SKF provides comprehensive interchange guides that cross-reference their bearings with equivalent models from other brands.
- Website Tools: Online tools and databases on the SKF website help find interchangeable bearings.
2. NSK
- Catalogs and Tools: NSK offers detailed catalogs and online tools to find equivalent bearings from other manufacturers.
- Engineering Support: NSK engineers can assist with finding suitable replacements.
3. FAG (Schaeffler Group)
- Interchangeability Resources: Schaeffler provides interchange tables and tools to cross-reference FAG bearings with other brands.
- Technical Support: Available for verifying compatibility and performance.
4. Timken
- Interchange Guides: Timken offers interchange guides and online resources to match Timken bearings with other brands.
- Customer Support: Timken’s technical support team can assist with interchange queries.
5. NTN
- Online Tools: NTN provides online interchange tools to find compatible bearings from other manufacturers.
- Catalogs: Detailed catalogs with interchange information are available.
6. INA (Schaeffler Group)
- Interchange Tools: Schaeffler’s tools and catalogs help cross-reference INA bearings with equivalents from other brands.
- Engineering Assistance: Technical support for interchangeability queries.
Summary
In summary, selecting the right bearings for the pulp and paper industry is crucial for ensuring the reliability, efficiency, and longevity of your machinery. By understanding the various types of bearings, their materials, lubrication requirements, and the importance of proper fits and internal clearances, you can make informed decisions that enhance your operational performance. Major bearing brands offer a range of specialized products designed to meet the demanding conditions of this industry, and knowing how to interchange these bearings effectively ensures minimal downtime and optimal functionality. At LOYAL, we are committed to providing high-quality, application-specific bearing solutions that cater to the unique needs of the pulp and paper industry, helping you achieve superior results and maintain the smooth running of your operations.