Mining and processing bearings play a vital role in the functionality and efficiency of mining equipment. Their design and construction are tailored to meet the rigorous demands of the mining industry, ensuring durability, reliability, and optimal performance. By choosing the right bearings and maintaining them properly, mining operations can achieve greater productivity, reduced downtime, and lower maintenance costs.
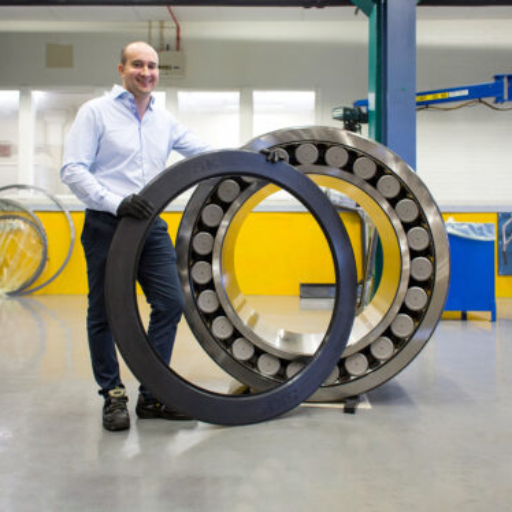
Types of Bearings Used in Mining and Processing Equipment
Mining and processing equipment rely on a variety of bearing types to support different functions and operational demands. Here is a classification of the main bearing types used in this industry:
1. Spherical Roller Bearings
Spherical roller bearings are designed to handle high radial and axial loads, as well as misalignment. They are commonly used in heavy-duty applications such as:
- Crushers:For managing high impact and vibration.
- Conveyors:To support heavy and continuous movement of materials.
2. Tapered Roller Bearings
Tapered roller bearings can handle both radial and axial loads. They are often used in applications where precision and stability are crucial:
- Grinding Mills:To support heavy loads and ensure precise alignment.
- Excavators:For stable and reliable operation under heavy load conditions.
3. Cylindrical Roller Bearings
Cylindrical roller bearings are ideal for high-speed applications and can support heavy radial loads. They are typically used in:
- Conveyors:For smooth and efficient material handling.
- Pumps:To ensure reliable operation in harsh environments.
4. Thrust Bearings
Thrust bearings are specifically designed to handle axial loads. They are essential in applications requiring support for high thrust forces:
- Excavators:To manage the axial loads during digging and lifting.
- Crushers:To support axial forces generated during crushing operations.
5. Ball Bearings
Ball bearings are versatile and can handle both radial and axial loads. They are used in a variety of applications where speed and precision are needed:
- Electric Motors:To ensure efficient and reliable motor operation.
- Gearboxes:For smooth transmission of power.
6. Needle Roller Bearings
Needle roller bearings are suitable for applications requiring high load capacity in a small footprint. They are used in:
- Hydraulic Pumps:To support high pressure and load conditions.
- Conveyor Systems:Where space constraints require compact bearing solutions.
7. Plain Bearings
Plain bearings, also known as bushings, are simple and robust, suitable for applications with heavy loads and low-speed movement:
- Loaders:For reliable operation under heavy loads and continuous movement.
- Drills:To withstand high axial loads and provide stability.
8. Self-aligning Ball Bearings
Self-aligning ball bearings are designed to accommodate misalignment and are used in applications where shaft deflection or mounting errors occur:
- Fans:For reliable and quiet operation despite misalignment.
- Vibrating Screens:To manage misalignment and ensure efficient operation.
Selecting the right type of bearing for mining and processing equipment is crucial for ensuring optimal performance and longevity. Each bearing type has its unique characteristics and applications, and understanding these can help in making informed decisions to enhance the efficiency and reliability of mining operations.
Importance of Bearing Quality
High-quality bearings are essential for minimizing downtime and maximizing productivity. Bearings from brands like Timken, SKF, and NTN are renowned for their durability and reliability. Proper maintenance and regular inspections are also crucial to ensure the longevity of the bearings and the equipment they support.
Selected Tapered Roller Bearings for Mining Equipment
Type |
Bore Diameter |
Outside Diameter |
Width |
Brand |
2788/2720 |
38.1 mm |
76.2 mm |
23.812 mm |
Timken |
2793/2720 |
34.925 mm |
76.2 mm |
23.774 mm |
Timken |
2789/2720 |
39.688 mm |
76.2 mm |
23.812 mm |
Timken |
2790/2720 |
39.688 mm |
76.2 mm |
23.774 mm |
SKF |
2794/2720 |
34.925 mm |
76.2 mm |
23.774 mm |
NTN |
2788A/2720 |
38.1 mm |
76.2 mm |
24.176 mm |
NTN |
2788B/2720 |
38.1 mm |
76.2 mm |
24.176 mm |
SKF |
Utilizing these robust and high-performance bearings can enhance the efficiency and reliability of mining operations.
Things to Note When Installing Bearings in Mining and Processing Equipment
Proper installation of bearings is critical to ensure the optimal performance and longevity of mining and processing equipment. Here are key considerations and steps to follow during the installation process:
1. Preparation
- Cleanliness:Ensure the installation area and tools are clean and free from dust, dirt, and contaminants. Even small particles can cause significant damage to bearings.
- Inspection:Check the bearing and housing for any visible damage or defects before installation. Ensure that the bearing is the correct type and size for the application.
2. Handling
- Proper Handling:Use appropriate tools and handling techniques to avoid damaging the bearing. Never strike a bearing directly with a hammer or use excessive force.
- Lubrication:Apply the recommended type and amount of lubricant to the bearing. Proper lubrication is crucial to reduce friction and wear.
3. Mounting
- Temperature Control:For interference fits, consider heating the bearing or cooling the shaft to facilitate easier installation. Use controlled methods such as an induction heater for heating the bearing.
- Alignment:Ensure the bearing is properly aligned with the shaft and housing. Misalignment can lead to premature bearing failure and equipment damage.
- Mounting Tools:Use the correct mounting tools, such as bearing presses, hydraulic nuts, or sleeves, to apply uniform pressure and avoid damage to the bearing.
4. Securing the Bearing
- Locking Mechanisms:Use the appropriate locking mechanisms (e.g., locknuts, set screws, or snap rings) to secure the bearing in place. Ensure that these are tightened to the manufacturer’s specified torque settings.
- Seals and Shields:Install any necessary seals or shields to protect the bearing from contaminants and retain lubrication.
5. Post-Installation Checks
- Rotation Test:After installation, rotate the bearing by hand to check for smoothness and proper seating. Any unusual resistance or noise may indicate misalignment or contamination.
- Lubrication Check:Ensure that the bearing has been adequately lubricated and that the lubrication system is functioning correctly.
6. Monitoring and Maintenance
- Regular Inspections:Conduct regular inspections to monitor bearing condition and performance. Look for signs of wear, noise, vibration, or excessive temperature.
- Relubrication:Follow the manufacturer’s recommendations for relubrication intervals and quantities. Use the correct type of lubricant as specified for the application.
Proper installation of bearings is essential for the reliable operation of mining and processing equipment. By following these guidelines and paying attention to details, you can ensure that the bearings perform optimally and have a long service life.
Problems That May Occur During Use of Bearings in Mining and Processing Equipment
Even with proper installation and maintenance, bearings in mining and processing equipment can encounter various problems during use. Understanding these potential issues can help in early detection and mitigation, ensuring the longevity and reliability of the equipment. Here are some common problems and their causes:
1. Excessive Wear and Tear
- Cause:Lack of proper lubrication, contamination, or misalignment.
- Symptoms:Increased noise, vibration, and heat generation.
- Solution:Regularly check and replenish lubrication, ensure proper alignment, and protect bearings from contaminants.
2. Bearing Overheating
- Cause:Insufficient lubrication, excessive load, or high ambient temperatures.
- Symptoms:Elevated temperature readings, discoloration of bearing surfaces.
- Solution:Use the correct type and amount of lubricant, verify load ratings, and provide adequate cooling or ventilation.
3. Contamination
- Cause:Ingress of dirt, dust, moisture, or other foreign particles.
- Symptoms:Rough operation, noise, and premature wear.
- Solution:Implement effective sealing solutions, maintain a clean working environment, and use clean, filtered lubricants.
4. Corrosion
- Cause:Exposure to moisture, chemicals, or corrosive environments.
- Symptoms:Rust on bearing surfaces, pitting, and flaking.
- Solution:Use corrosion-resistant bearings, apply protective coatings, and control environmental exposure.
5. Fatigue Failure
- Cause:Repeated loading cycles exceeding the bearing’s fatigue limit.
- Symptoms:Cracks in bearing material, spalling, and eventual fracture.
- Solution:Ensure proper load distribution, use bearings designed for high-cycle fatigue, and regularly inspect for early signs of fatigue.
6. Misalignment
- Cause:Improper installation, shaft deflection, or structural deformation.
- Symptoms:Uneven wear patterns, increased noise, and vibration.
- Solution:Verify proper alignment during installation, use self-aligning bearings if necessary, and inspect the structural integrity of the equipment.
7. Inadequate Lubrication
- Cause:Incorrect lubricant type, insufficient lubricant amount, or extended relubrication intervals.
- Symptoms:Increased friction, heat, and wear.
- Solution:Follow manufacturer’s lubrication recommendations, monitor lubricant levels, and establish a regular lubrication schedule.
Understanding the common problems that can occur during the use of bearings in mining and processing equipment is crucial for maintaining their performance and longevity. Regular inspection, proper maintenance, and timely interventions can help mitigate these issues, ensuring the efficient and reliable operation of your equipment.
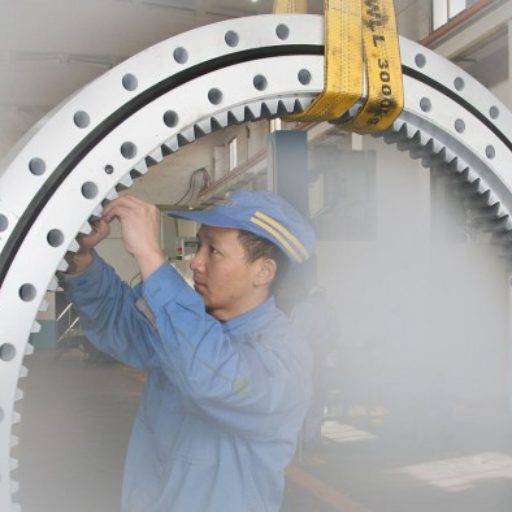
Product Clearance Requirements for Bearings in Mining and Processing Equipment
Proper clearance in bearings is crucial for optimal performance, longevity, and reliability, especially in demanding environments such as mining and processing operations. Clearance refers to the total distance through which one bearing ring can be moved relative to the other, either radially (radial clearance) or axially (axial clearance). Here’s an explanation of the key aspects of product clearance requirements:
1. Radial Clearance
Radial clearance is the total movement of the bearing’s inner ring relative to the outer ring in the radial direction. It is essential to ensure proper load distribution, thermal expansion accommodation, and lubrication.
- Normal Clearance:Suitable for general applications where operating conditions are standard. Provides a balance between load-carrying capacity and operational smoothness.
- Increased Clearance (C3, C4):Required for high-temperature environments, heavy loads, or where thermal expansion is significant. Allows for better performance under thermal growth and shock loads.
- Reduced Clearance (C2):Used in high-precision applications where tighter control over shaft positioning is necessary. Ensures minimal play and higher accuracy.
2. Axial Clearance
Axial clearance refers to the total movement of the bearing’s inner ring relative to the outer ring in the axial direction. It is vital for managing axial loads and accommodating thermal expansion along the shaft.
- Normal Axial Clearance:Suitable for applications with balanced axial loads and standard thermal conditions.
- Increased Axial Clearance:Necessary for applications experiencing higher axial loads or significant thermal elongation. Ensures the bearing can accommodate changes without binding.
- Reduced Axial Clearance:Applied in precision equipment where axial play needs to be minimized for higher accuracy and stability.
3. Factors Affecting Clearance Requirements
- Operating Temperature:Bearings expand with heat, which can reduce internal clearance. Bearings in high-temperature applications may require increased clearance to compensate for thermal expansion.
- Load Conditions:Heavy radial or axial loads can compress the bearing components, reducing clearance. Bearings in such conditions may need increased initial clearance.
- Speed:High-speed applications may generate additional heat, impacting the bearing clearance. Appropriate clearance ensures smooth operation at high speeds.
- Precision and Application:Precision machinery or applications requiring exact positioning may need reduced clearance for better control and stability.
4. Setting and Measuring Clearance
- Setting Clearance:Proper clearance is set during the bearing selection and installation process. It involves choosing the correct bearing type and class based on the specific application requirements.
- Measuring Clearance:Clearance can be measured using feeler gauges, dial indicators, or specialized tools provided by bearing manufacturers. Accurate measurement ensures that the bearing will perform as expected under operational conditions.
5. Impact of Incorrect Clearance
- Insufficient Clearance:Can lead to excessive friction, heat generation, and premature bearing failure. It may cause the bearing to seize under load or thermal expansion.
- Excessive Clearance:May result in increased vibration, noise, and reduced precision. It can lead to uneven load distribution and accelerated wear of bearing components.
Proper product clearance is vital for the performance and durability of bearings in mining and processing equipment. Understanding and setting the correct radial and axial clearances based on operational conditions and application requirements can significantly enhance bearing life and equipment reliability.
Product Sealing Requirements for Bearings in Mining and Processing Equipment
Sealing is a critical aspect of bearing performance in mining and processing equipment, as it protects the bearings from contaminants and retains lubrication. Here are the key points to consider regarding product sealing requirements:
1. Protection from Contaminants
- Dust and Dirt:Mining environments are typically dusty, and even small particles can cause significant damage to bearings. Effective seals prevent dust and dirt from entering the bearing.
- Moisture and Water:Bearings must be protected from water ingress, which can lead to corrosion and lubricant degradation. Seals help keep moisture out.
- Chemical Exposure:In some processing environments, chemicals can be harmful to bearings. Seals designed to resist chemical exposure are essential.
2. Lubrication Retention
- Lubricant Leakage Prevention:Proper seals prevent lubricants from leaking out of the bearing assembly, ensuring continuous lubrication and reducing the need for frequent maintenance.
- Contaminant Exclusion:Seals keep contaminants out while retaining the lubricant inside, maintaining the bearing’s efficiency and lifespan.
3. Types of Seals
- Contact Seals:Provide a tight barrier by contacting the bearing surfaces directly. They are effective in keeping out contaminants but can add friction and heat.
- Non-Contact Seals:Utilize a small gap to form a barrier, allowing for higher speeds with less friction. They offer good protection against large particles and moderate contaminants.
- Labyrinth Seals:Consist of multiple passages that create a complex path for contaminants to navigate, providing excellent protection with minimal friction.
- Shielded Bearings:Incorporate metal shields that offer protection against larger particles and moderate contaminants, suitable for less severe environments.
4. Environmental Considerations
- Harsh Environments:Bearings in extremely dusty or wet conditions require robust sealing solutions, such as multiple seals or heavy-duty contact seals.
- High Temperatures:Seals must be made of materials that can withstand high temperatures without degrading, ensuring long-term effectiveness.
- Dynamic Conditions:In applications with high-speed or oscillating movements, seals must be designed to handle dynamic loads and maintain their integrity.
5. Maintenance and Inspection
- Regular Checks:Periodic inspection of seals for wear, damage, or degradation is essential to ensure they continue to provide effective protection.
- Replacement:Seals should be replaced as part of routine maintenance whenever they show signs of wear or at scheduled intervals to prevent bearing contamination.
Sealing requirements are crucial for the protection and efficient operation of bearings in mining and processing equipment. By choosing the right type of seal and ensuring regular maintenance, you can significantly extend the lifespan of the bearings, reduce downtime, and maintain the reliability of your equipment.
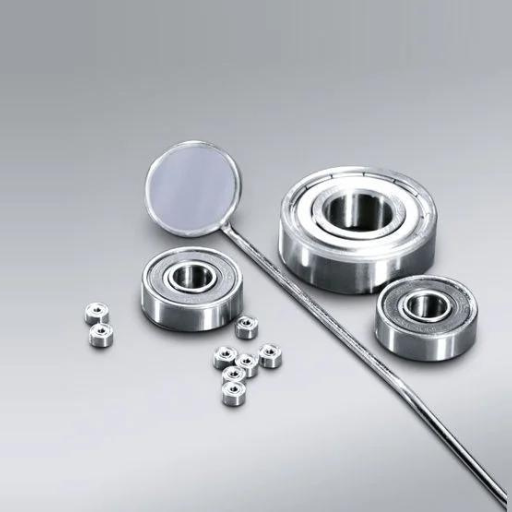
Usage Environment Requirements for Bearings in Mining and Processing Equipment
Bearings used in mining and processing equipment are subjected to extreme and challenging environments. Ensuring that they can withstand these conditions is crucial for their performance and longevity. Here are the key environmental requirements to consider:
1. Temperature Extremes
- High Temperatures:Bearings must be capable of operating at high temperatures generated by friction and external heat sources. Materials and lubricants used should withstand thermal expansion and heat without degrading.
- Low Temperatures:In cold environments, bearings should remain functional without becoming brittle or losing lubrication effectiveness.
2. Contaminants
- Dust and Dirt:Bearings must be protected from dust and dirt, which are prevalent in mining environments. Seals and shields are essential to prevent contaminants from entering the bearing.
- Water and Moisture:Bearings should be resistant to water ingress, which can cause corrosion and lubricant degradation. Effective sealing solutions are necessary to keep moisture out.
3. Load and Vibration
- Heavy Loads:Bearings must support significant radial and axial loads common in mining and processing equipment. They should be designed to handle heavy impacts and continuous operational stresses.
- Vibration and Shock:Bearings should be capable of withstanding constant vibration and occasional shock loads without suffering damage or performance degradation.
4. Chemical Exposure
- Corrosive Substances:Bearings may be exposed to chemicals and corrosive substances in processing environments. Materials used should be resistant to corrosion and chemical attack.
5. Lubrication Conditions
- Adequate Lubrication:Bearings must be adequately lubricated to reduce friction and wear. Lubricants should be suitable for the specific environmental conditions and application requirements.
- Contaminant-Free Lubrication:Lubricants should remain clean and free from contaminants. Sealing systems should effectively retain lubricants and prevent contamination.
Bearings in mining and processing equipment must meet stringent environmental requirements to perform reliably under extreme conditions. By addressing factors such as temperature, contaminants, load, vibration, and lubrication, you can ensure the bearings’ durability and efficiency, ultimately enhancing the productivity and reliability of your equipment.
Temperature Requirements for Bearings in Mining and Processing Equipment
Bearings in mining and processing equipment must operate effectively under a wide range of temperatures. Meeting these temperature requirements is essential for ensuring the reliability and longevity of the bearings. Here are the key points to consider:
1. High-Temperature Tolerance
- Heat Resistance:Bearings must be able to withstand high temperatures generated by friction, heavy loads, and external heat sources without losing their structural integrity or performance.
- Material Selection:High-temperature bearings are often made from special alloys and are treated with heat-resistant coatings to prevent thermal degradation.
- Lubrication:High-temperature lubricants are essential to maintain proper lubrication and minimize wear. These lubricants should not degrade or evaporate at elevated temperatures.
2. Low-Temperature Operation
- Cold Resistance:Bearings must remain functional in low-temperature environments without becoming brittle or losing their load-carrying capacity.
- Materials and Lubricants:Low-temperature bearings may use special materials and lubricants designed to perform in cold conditions, ensuring smooth operation and reduced friction.
3. Thermal Expansion Accommodation
- Expansion and Contraction:Bearings should be designed to accommodate thermal expansion and contraction of components, preventing excessive stress and misalignment.
- Clearance Adjustments:Appropriate internal clearance settings are crucial to allow for temperature-induced changes in bearing dimensions, ensuring smooth operation under varying temperatures.
4. Consistent Performance
- Operational Stability:Bearings should maintain consistent performance across the temperature range, ensuring reliability and efficiency in both high and low-temperature conditions.
- Sealing Solutions:Effective seals are necessary to protect bearings from temperature-induced contamination and to retain lubricants.
Temperature requirements are critical for the performance of bearings in mining and processing equipment. Bearings must be designed to handle high and low temperatures, accommodate thermal expansion, and maintain consistent performance.
Example Data for Lubricant Selection:
Parameter |
Example Value |
Operating Temperature |
-20°C to 150°C (-4°F to 302°F) |
Extreme Temperature |
Up to 200°C (392°F), down to -40°C (-40°F) |
Load Type |
Heavy radial load, occasional axial thrust |
Load Magnitude |
5000 N radial, 2000 N axial |
Speed |
1500 RPM |
Environment |
High dust, occasional water exposure |
Humidity |
60% relative humidity |
Lubricant Type |
Grease (for easier maintenance) |
Viscosity |
ISO VG 220 |
Additives |
EP additives (Extreme Pressure) |
Re-lubrication Interval |
Every 500 hours or 3 months |
Compatibility |
Synthetic grease compatible with rubber seals and steel bearings |
Example Data for Bearing Selection:
Application |
Load Type |
Speed |
Environment |
Temperature |
Recommended Bearing Type |
Conveyors |
Radial, Moderate Axial |
Moderate |
Dusty |
-20°C to 80°C |
Spherical Roller Bearings |
Crushers |
Heavy Radial, High Axial |
Low |
Dusty, Wet |
-20°C to 100°C |
Tapered Roller Bearings, Thrust Bearings |
Grinding Mills |
Heavy Radial |
Moderate |
Dusty |
-20°C to 150°C |
Cylindrical Roller Bearings |
Drilling Equipment |
High Axial |
Low |
Dusty, Wet |
-20°C to 80°C |
Thrust Bearings, Tapered Roller Bearings |
Electric Motors |
Moderate Radial, Low Axial |
High |
Clean to Moderate Dust |
-20°C to 120°C |
Deep Groove Ball Bearings |
Fans |
Low to Moderate Radial |
High |
Moderate Dust |
-20°C to 100°C |
Deep Groove Ball Bearings |
Excavators |
Heavy Radial, Moderate Axial |
Low |
Dusty, Wet |
-20°C to 80°C |
Spherical Roller Bearings, Plain Bearings |
Bearing Life Data in Mining and Processing Equipment
Bearing life is a critical parameter in the selection and maintenance of bearings in mining and processing equipment. Understanding the factors that influence bearing life and how to calculate it can help in ensuring the reliability and longevity of the equipment.
Practical Bearing Life Data
Parameter |
Example Value |
Basic Dynamic Load Rating (C) |
100,000 N |
Equivalent Dynamic Load (P) |
25,000 N |
Operating Speed (n) |
1500 RPM |
L10 Life (in hours) |
20,000 hours at given speed and load |
Lubrication Interval |
Every 500 hours or 3 months |
Operating Temperature Range |
-20°C to 150°C |
Contamination Control |
Sealed bearings, regular maintenance |
Summary of Basic Dynamic Load Rating and Fatigue Life
Basic Dynamic Load Rating (C)
- Definition:Represents the bearing’s capacity to withstand dynamic loads. It is the constant radial load under which a group of identical bearings with a stationary outer ring can endure for 1 million revolutions.
- Unit:Expressed in Newtons (N).
- Importance:Determines the bearing’s suitability for specific applications, ensuring it can handle operational loads without premature failure.
- Source:Provided by bearing manufacturers based on standardized testing.
Fatigue Life (L10 Life)
Definition: Indicates the number of revolutions at which 90% of a group of identical bearings will still be operational without fatigue. It measures the bearing’s reliability and durability under specified conditions.
Unit: Expressed in millions of revolutions or hours of operation at a given speed.
Calculation:
- L10=(CP)3×106 revolutionsL_{10} = \left(\frac{C}{P}\right)^3 \times 10^6 \text{ revolutions}L10=(PC)3×106 revolutions
Where:
-
- L10L_{10}L10 = Basic rating life in millions of revolutions
- CCC = Basic dynamic load rating (N)
- PPP = Equivalent dynamic bearing load (N)
Equivalent Dynamic Bearing Load (P): Calculated considering actual operational loads and conditions.
- P=X⋅Fr+Y⋅FaP = X \cdot F_r + Y \cdot F_aP=X⋅Fr+Y⋅Fa
Where:
-
- FrF_rFr = Radial load (N)
- FaF_aFa = Axial load (N)
- XXX and YYY = Load factors based on bearing type and conditions
Adjusted Rating Life (L10m)
- Purpose:Accounts for various operating conditions like lubrication quality, temperature, and contamination, providing a more accurate estimate of bearing life.
- Calculation:L10m=a1×a2×a3×L10L_{10m} = a_1 \times a_2 \times a_3 \times L_{10}L10m=a1×a2×a3×L10 Where:
- a1a_1a1 = Life adjustment factor for reliability
- a2a_2a2 = Life adjustment factor for material
- a3a_3a3 = Life adjustment factor for operating conditions
The basic dynamic load rating (C) and fatigue life (L10) are fundamental parameters in bearing selection for mining and processing equipment. They ensure the bearing can handle the expected loads and conditions, providing reliable and long-lasting performance.
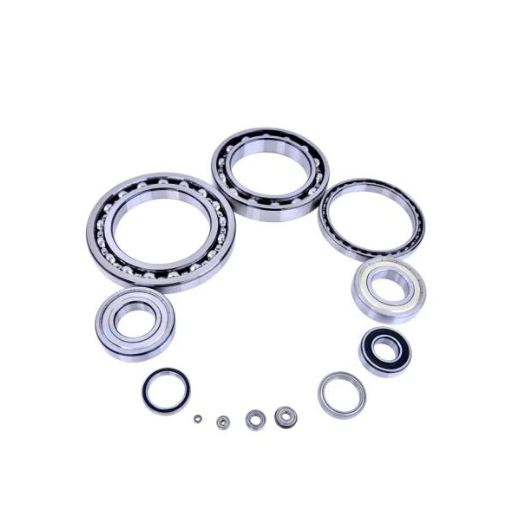
Dynamic Equivalent Load (P)
Definition
The dynamic equivalent load (P) is a theoretical load value that represents the combined effects of both radial and axial loads acting on a bearing. It is used to simplify the analysis of complex load situations by converting them into a single load value. This load is crucial for calculating the bearing’s fatigue life and ensuring its suitability for the application.
Importance
- Load Simplification:Combines radial and axial loads into a single value for easier analysis and calculation.
- Bearing Life Calculation:Essential for determining the fatigue life (L10) of the bearing.
- Application Suitability:Helps in selecting the appropriate bearing type and size for specific operating conditions.
Calculation
Where:
- PPP = Dynamic equivalent load (N)
- FrF_rFr = Actual radial load (N)
- FaF_aFa = Actual axial load (N)
- XXX and YYY = Load factors, which depend on the type of bearing and the load direction
Load Factors (X and Y)
- Radial Bearings:For bearings primarily carrying radial loads, XXX is generally close to 1, and YYY is relatively small.
- Axial Bearings:For bearings primarily carrying axial loads, XXX may be smaller, and YYY can be larger to account for the significant axial component.
The dynamic equivalent load (P) is a vital parameter in bearing selection and analysis, providing a simplified approach to understanding and managing complex load conditions.
Basic Static Load Ratings and Static Equivalent Loads
Basic Static Load Rating (C0)
- Definition:The basic static load rating (C0) is the maximum load that a bearing can withstand without permanent deformation. This load rating considers both radial and axial loads that cause plastic deformation at the contact points between the rolling elements and raceways.
- Unit:Expressed in Newtons (N).
- Importance:Indicates the bearing’s ability to support heavy, non-rotating loads or very slow-moving loads without suffering permanent damage.
- Source:Provided by bearing manufacturers based on standardized testing and calculations.
Static Equivalent Load (P0)
- Definition:The static equivalent load (P0) is a calculated value that combines the actual radial and axial loads acting on a bearing into a single load value, representing the overall load that causes the same amount of deformation as the actual loads.
- Importance:Used to determine if the bearing can support the applied loads without exceeding its static load rating (C0) and to ensure the bearing does not suffer permanent deformation under static conditions.
Load Factors (X0 and Y0)
- Radial Bearings:For bearings primarily carrying radial loads, X0X_0X0 is generally close to 1, and Y0Y_0Y0 is relatively small.
- Axial Bearings:For bearings primarily carrying axial loads, X0X_0X0 may be smaller, and Y0Y_0Y0 can be larger to account for the significant axial component.
Practical Example
Given Data:
- Basic Static Load Rating (C0):120,000 N
- Actual Radial Load (F_r):30,000 N
- Actual Axial Load (F_a):10,000 N
- Load Factors (X0, Y0):6, 1.2
Understanding basic static load ratings (C0) and static equivalent loads (P0) is essential for selecting the appropriate bearing for applications with heavy, non-rotating, or slow-moving loads. These parameters ensure that the bearing can support the applied loads without experiencing permanent deformation, maintaining the integrity and reliability of the equipment.
Bearing Tolerances
Definition
Bearing tolerances refer to the permissible variations in the dimensions and geometry of a bearing. These tolerances ensure that bearings fit properly and function efficiently within mechanical assemblies.
Importance
- Precision:Ensures bearings meet specific dimensional and performance requirements.
- Interchangeability:Allows bearings to be replaced or interchanged without custom adjustments.
- Performance:Ensures optimal load distribution, reduced friction, and prolonged bearing life.
- Reliability:Minimizes operational issues related to misalignment, noise, and vibration.
Types of Tolerances
Dimensional Tolerances:
- Inner and Outer Diameter:Controls the fit between the bearing and shaft or housing.
- Width:Ensures the bearing maintains proper axial positioning.
- Bore Diameter:Critical for shaft fit and rotational accuracy.
Geometric Tolerances:
- Roundness:Ensures the bearing’s rolling elements and raceways are perfectly circular to minimize vibration and noise.
- Cylindricity:Ensures the inner and outer rings are uniformly cylindrical to avoid uneven load distribution.
- Parallelism:Maintains alignment between bearing components to reduce stress and wear.
Tolerance Classes
Bearings are classified into various tolerance classes based on precision. The most common standards are set by ISO (International Organization for Standardization) and ABEC (Annular Bearing Engineers’ Committee).
- ISO Tolerance Classes:Ranges from P0 (normal) to P2 (high precision), with intermediate classes like P6 and P5.
- ABEC Tolerance Classes:Ranges from ABEC 1 (lowest precision) to ABEC 9 (highest precision).
Bearing tolerances are crucial for ensuring that bearings fit correctly and operate efficiently within machinery. They encompass dimensional and geometric tolerances, which are standardized to facilitate interchangeability and reliability.
Fits and Internal Clearances in Bearings
Fits
Definition: Fits refer to the relationship between the dimensions of the bearing and its mating components (shaft and housing). Proper fits ensure that bearings are securely positioned and operate efficiently without excessive play or stress.
Types of Fits:
Interference Fit (Press Fit):
- Description:The bearing’s inner or outer ring is slightly larger than the shaft or housing bore, requiring force for assembly.
- Applications:Used in applications where high stability and rigidity are needed, such as heavy machinery.
- Example:The inner ring of a bearing pressed onto a shaft.
Transition Fit:
- Description:Falls between interference and clearance fits, providing a balance between ease of assembly and stability.
- Applications:Suitable for applications where moderate stability is required.
- Example:A bearing that can be easily assembled by hand but remains firmly in place during operation.
Clearance Fit (Loose Fit):
- Description:The bearing’s inner or outer ring is slightly smaller than the shaft or housing bore, allowing for easy assembly and disassembly.
- Applications:Used in applications where frequent removal or adjustment is needed.
- Example:Bearings in adjustable mechanisms or those subjected to thermal expansion.
Internal Clearances
Definition: Internal clearance is the total distance through which one bearing ring can be moved relative to the other, either radially or axially. It is crucial for accommodating thermal expansion, ensuring proper load distribution, and maintaining bearing performance.
Types of Internal Clearances:
Radial Clearance:
- Description:The total radial distance one ring can move relative to the other.
- Categories:C2 (less than normal), C0 (normal), C3 (greater than normal), C4, and C5 (even greater than C3).
- Applications:Different categories are selected based on operating conditions such as load, temperature, and speed.
Axial Clearance:
- Description:The total axial distance one ring can move relative to the other.
- Importance:Critical in applications with significant axial loads or misalignment.
Factors Influencing Internal Clearance:
- Temperature:Bearings expand with heat, which can reduce clearance. Higher operating temperatures may require greater initial clearance.
- Load:Heavy loads can compress the bearing components, reducing clearance.
- Speed:High-speed applications may generate additional heat, affecting clearance.
Proper fits and internal clearances are essential for the optimal performance and longevity of bearings. Fits ensure that bearings are securely positioned within their assemblies, while internal clearances accommodate operational conditions such as thermal expansion and load variations.
Lubrication for Bearings in Mining and Processing Equipment
Definition
Lubrication is the process of applying a lubricant to the moving parts of a bearing to reduce friction, wear, and heat generation. Proper lubrication is essential for the efficient operation and longevity of bearings in mining and processing equipment.
Importance
- Reduces Friction:Minimizes the resistance between moving parts, ensuring smooth operation.
- Prevents Wear:Reduces the wear and tear of bearing components, extending their lifespan.
- Dissipates Heat:Helps in dissipating the heat generated due to friction, preventing overheating.
- Protects Against Contaminants:Creates a barrier that helps keep dust, dirt, and moisture away from the bearing surfaces.
- Prevents Corrosion:Forms a protective layer that prevents rust and corrosion on bearing surfaces.
Types of Lubricants
Grease:
- Composition:A semi-solid lubricant composed of a base oil, thickener, and additives.
- Applications:Used in bearings where relubrication is infrequent or difficult.
- Advantages:Easy to apply, stays in place, good for sealing out contaminants.
- Disadvantages:Can create more friction than oil, limited cooling ability.
Oil:
- Composition:A liquid lubricant that can be mineral-based, synthetic, or a blend.
- Applications:Used in high-speed or high-temperature applications where effective cooling is necessary.
- Advantages:Excellent cooling properties, lower friction, can be easily filtered and replaced.
- Disadvantages:Requires a more complex lubrication system, can leak out of the bearing.
Solid Lubricants:
- Composition:Materials like graphite, molybdenum disulfide, or PTFE.
- Applications:Used in extreme conditions where liquid lubricants would fail, such as very high temperatures or vacuum environments.
- Advantages:Can function in harsh conditions, provides long-lasting lubrication.
- Disadvantages:Limited to specific applications, not suitable for all bearing types.
Lubrication Methods
Manual Lubrication:
- Description:Applying lubricant by hand using grease guns or oil cans.
- Applications:Suitable for small-scale operations or where automatic systems are not feasible.
- Advantages:Simple and cost-effective for infrequent lubrication needs.
- Disadvantages:Labor-intensive, inconsistent application.
Automatic Lubrication:
- Description:Using automated systems to supply lubricant at regular intervals.
- Applications:Ideal for large-scale operations with many bearings.
- Advantages:Consistent lubrication, reduces maintenance labor, can be monitored and controlled.
- Disadvantages:Higher initial cost, requires installation and maintenance.
Centralized Lubrication:
- Description:A system where lubricant is supplied to multiple bearings from a central reservoir.
- Applications:Suitable for complex machinery with many lubrication points.
- Advantages:Efficient, reduces downtime, ensures all bearings are properly lubricated.
- Disadvantages:Can be complex to install and maintain, higher initial cost.
Best Practices
- Choose the Right Lubricant:Select the appropriate type and grade of lubricant based on the bearing’s operating conditions.
- Regular Monitoring:Check lubricant levels and quality regularly to ensure proper lubrication.
- Maintain Cleanliness:Keep the lubrication system and bearings free from contaminants.
- Follow Manufacturer Guidelines:Adhere to the bearing and lubricant manufacturers’ recommendations for lubrication intervals and quantities.
Proper lubrication is essential for the performance and durability of bearings in mining and processing equipment. By selecting the right lubricant and applying it correctly, you can significantly reduce friction, wear, and heat, thereby extending the life of the bearings and ensuring the reliability of the equipment.
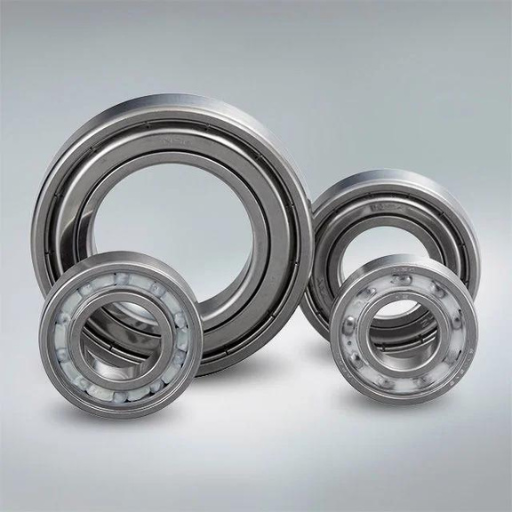
Materials for Bearing Rings and Rolling Elements
Bearing Rings
Chrome Steel (AISI 52100)
- Composition:High carbon chromium alloy steel.
- Properties:Excellent hardness, high wear resistance, and good fatigue strength.
- Applications:Commonly used for most standard bearing applications due to its durability and cost-effectiveness.
- Advantages:High load capacity, good surface finish, and consistent performance.
- Disadvantages:Susceptible to corrosion if not properly protected.
Stainless Steel (AISI 440C)
- Composition:High carbon stainless steel with chromium.
- Properties:Corrosion-resistant, good hardness, and moderate wear resistance.
- Applications:Suitable for applications in corrosive environments, such as food processing, marine, and medical industries.
- Advantages:Resistant to rust and corrosion, maintains strength in harsh environments.
- Disadvantages:More expensive than chrome steel, slightly lower fatigue strength.
Through-Hardened Steel
- Composition:Steel that has been heat-treated to achieve uniform hardness throughout.
- Properties:Consistent hardness and strength throughout the material.
- Applications:Used in applications requiring high impact resistance and toughness.
- Advantages:Uniform properties provide consistent performance.
- Disadvantages:Higher manufacturing cost compared to surface-hardened steel.
Case-Hardened Steel
- Composition:Steel with a hard surface layer and a tougher core.
- Properties:Combines a hard, wear-resistant surface with a tough, impact-resistant core.
- Applications:Ideal for heavy-duty applications where high wear resistance and toughness are needed.
- Advantages:Excellent wear resistance on the surface, high impact resistance in the core.
- Disadvantages:More complex manufacturing process.
Rolling Elements
Chrome Steel (AISI 52100)
- Properties:High hardness, excellent wear resistance, and good fatigue life.
- Applications:Widely used for balls and rollers in standard bearings.
- Advantages:Consistent performance, cost-effective.
- Disadvantages:Susceptible to corrosion without proper protection.
Stainless Steel (AISI 440C)
- Properties:Corrosion-resistant, good hardness, and moderate wear resistance.
- Applications:Used in environments where corrosion resistance is crucial.
- Advantages:Resistant to rust and corrosion, maintains integrity in harsh conditions.
- Disadvantages:Higher cost compared to chrome steel, slightly lower fatigue strength.
Ceramic Materials (Silicon Nitride, Si3N4)
- Properties:Extremely hard, lightweight, corrosion-resistant, and low thermal expansion.
- Applications:High-speed and high-temperature applications, such as aerospace, medical devices, and high-precision equipment.
- Advantages:High-speed capability, excellent thermal stability, and corrosion resistance.
- Disadvantages:High cost, brittleness compared to steel.
Carbon Steel
- Properties:Good strength and affordability, moderate hardness.
- Applications:Used in low-cost, low-load applications.
- Advantages:Economical, easy to machine.
- Disadvantages:Lower wear resistance and fatigue strength compared to alloy steels.
The choice of materials for bearing rings and rolling elements is crucial for the performance, durability, and suitability of bearings in various applications. Chrome steel and stainless steel are commonly used for their balance of hardness, wear resistance, and cost-effectiveness.
Introduction to Mining and Processing Bearing Brands
In the mining and processing industry, selecting the right bearing brand is crucial for ensuring the reliability and efficiency of equipment. Different brands offer various features, materials, and technologies tailored to specific applications. Here’s an introduction to some of the leading brands and the differences between them:
1. SKF
- Overview:SKF is a global leader in bearing manufacturing, known for its high-quality products and innovative solutions.
- Strengths:
- Advanced research and development.
- Comprehensive range of bearing types and sizes.
- Strong focus on sustainability and energy efficiency.
- Technologies:
- SKF Explorer performance class bearings.
- Integrated lubrication solutions.
- Condition monitoring systems.
2. NSK
- Overview:NSK is a prominent bearing manufacturer with a strong reputation for precision and reliability.
- Strengths:
- High precision and quality control.
- Wide range of bearings for various industries.
- Strong after-sales support and technical assistance.
- Technologies:
- Tough Steel technology for extended life in contaminated environments.
- NSK asset improvement program (AIP) for optimizing machinery performance.
- Advanced sealing solutions for enhanced protection.
3. Timken
- Overview:Timken is known for its high-performance bearings, particularly in heavy-duty and industrial applications.
- Strengths:
- Expertise in tapered roller bearings.
- Robust design suitable for extreme conditions.
- Strong focus on material science and metallurgy.
- Technologies:
- Timken UltraWind tapered roller bearings for wind energy applications.
- Wear-resistant coatings and finishes.
- Condition monitoring and predictive maintenance solutions.
4. FAG (Schaeffler Group)
- Overview:FAG, part of the Schaeffler Group, is renowned for its precision engineering and comprehensive product range.
- Strengths:
- Innovation in bearing design and manufacturing.
- Extensive application engineering support.
- High reliability and performance in demanding environments.
- Technologies:
- X-life bearings for extended service life.
- Advanced simulation and calculation tools for bearing design.
- High-performance lubricants and lubrication systems.
5. NTN
- Overview:NTN is a global manufacturer known for its durable and high-performance bearings.
- Strengths:
- Strong focus on research and development.
- Wide range of products for industrial and automotive applications.
- Emphasis on high-quality materials and manufacturing processes.
- Technologies:
- NTN ULTAGE series for high performance and reliability.
- Self-lubricating bearings for reduced maintenance.
- Precision bearings for high-speed and high-temperature applications.
6. NACHI
- Overview:NACHI provides a broad spectrum of bearings with a focus on innovation and quality.
- Strengths:
- Vertical integration from steel production to finished products.
- High-performance bearings for various industries.
- Strong commitment to continuous improvement.
- Technologies:
- NACHI Quest bearings for superior performance.
- High-capacity cylindrical roller bearings.
- Advanced heat treatment processes for enhanced durability.
Choosing the right bearing brand for mining and processing equipment involves considering the specific requirements of the application, such as load capacity, environmental conditions, and maintenance needs. Leading brands like SKF, NSK, Timken, FAG, NTN, and NACHI offer a range of high-quality bearings with unique features and technologies.
Applications of Bearing Brands in Mining and Processing Fields
Different bearing brands cater to various applications in the mining and processing fields, each offering specialized solutions to address the specific challenges of these industries. Here’s a look at how leading bearing brands are applied in mining and processing:
1. SKF
Applications:
- Crushers and Grinding Mills:SKF bearings are used in crushers and grinding mills to handle heavy radial and axial loads, ensuring efficient crushing and grinding of ores.
- Conveyors:SKF bearings help maintain smooth operation and reduce downtime in conveyor systems, essential for material handling in mining operations.
- Fans and Pumps:SKF bearings provide reliability and long service life in ventilation fans and pumps, crucial for maintaining air quality and fluid movement.
- Electric Motors:SKF bearings ensure the efficient operation of electric motors used in various mining equipment.
Technologies:
- SKF Explorer bearings for high performance and extended life.
- Integrated lubrication solutions to reduce maintenance.
2. NSK
Applications:
- Excavators and Loaders:NSK bearings are used in the joints and rotating parts of excavators and loaders, providing high durability and resistance to heavy shock loads.
- Screening Equipment:NSK bearings ensure reliable operation and reduce vibration in screening equipment used for sorting materials.
- Gearboxes:NSK bearings support the smooth and efficient operation of gearboxes in mining machinery, ensuring reliable power transmission.
Technologies:
- Tough Steel bearings for enhanced wear resistance in contaminated environments.
- Advanced sealing solutions for protection against dust and water.
3. Timken
Applications:
- Draglines and Shovels:Timken bearings are designed for the heavy-duty requirements of draglines and shovels, providing robustness and longevity under severe loads.
- Haul Trucks:Timken bearings ensure the reliable operation of wheel hubs and suspension systems in haul trucks, handling heavy loads and rough terrain.
- Crushing Equipment:Timken tapered roller bearings support the high axial and radial loads in crushing equipment, ensuring efficient ore processing.
Technologies:
- Wear-resistant coatings for extended bearing life.
- Condition monitoring systems for predictive maintenance.
4. FAG (Schaeffler Group)
Applications:
- Grinding Mills:FAG bearings support the rotating elements in grinding mills, providing high reliability and performance under heavy loads.
- Conveyors and Material Handling:FAG bearings are used in conveyor systems, ensuring smooth and continuous operation.
- Flotation Cells:FAG bearings ensure the efficient operation of flotation cells used in ore processing, handling both radial and axial loads.
Technologies:
- X-life bearings for longer service life and higher performance.
- High-performance lubricants to reduce friction and wear.
5. NTN
Applications:
- Bucket Wheel Excavators:NTN bearings provide the durability and load capacity needed for bucket wheel excavators used in large-scale mining operations.
- Processing Equipment:NTN bearings are used in various processing equipment, including crushers, screens, and separators, ensuring efficient material processing.
- Stacker Reclaimers:NTN bearings ensure the reliable operation of stacker reclaimers, essential for bulk material handling in mining sites.
Technologies:
- ULTAGE series for high performance and reliability.
- Self-lubricating bearings to reduce maintenance needs.
6. NACHI
Applications:
- Drilling Equipment:NACHI bearings are used in drilling equipment, providing high resistance to shock loads and contamination.
- Crushers:NACHI bearings support the heavy loads and high impact conditions in crushing equipment, ensuring efficient ore processing.
- Conveyors:NACHI bearings ensure reliable operation and reduce downtime in conveyor systems used for transporting materials.
Technologies:
- NACHI Quest bearings for superior performance.
- Advanced heat treatment processes for enhanced durability.
Each bearing brand brings unique strengths and technologies to various applications in the mining and processing fields. From heavy-duty load handling in crushers and excavators to reliable operation in conveyors and processing equipment, these brands offer tailored solutions to meet the demanding conditions of the mining industry.
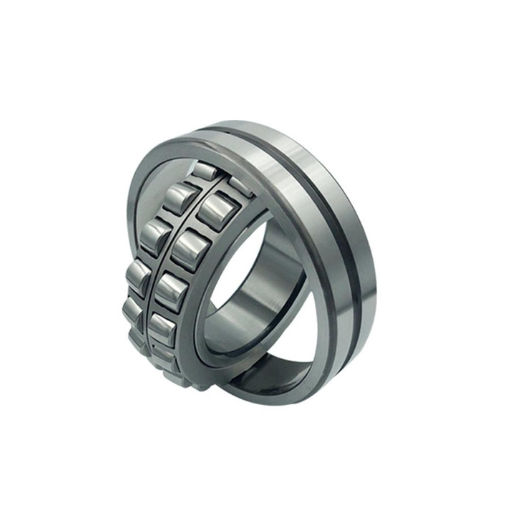
Interchange Between Bearing Brands
Interchanging bearings between different brands can be complex due to variations in product specifications, materials, and technologies. However, leading bearing manufacturers such as SKF, NSK, Timken, FAG (Schaeffler Group), NTN, and NACHI provide products that are often interchangeable based on standardized dimensions and performance characteristics. Here’s a guide to understanding the interchangeability of different types of bearings among these brands:
1. Ball Bearings
Deep Groove Ball Bearings:
- SKF:6200, 6300, 6400 series
- NSK:6200, 6300, 6800 series
- Timken:9100, 9300, 9700 series
- FAG:6200, 6300, 6400 series
- NTN:6200, 6300, 6800 series
- NACHI:6200, 6300, 6800 series
Interchangeability:
- Bearings in the 6200, 6300, and 6800 series are generally interchangeable across brands, with dimensional and load capacity similarities.
Angular Contact Ball Bearings:
- SKF:7200, 7300 series
- NSK:7200, 7300 series
- Timken:2MM, 3MM series
- FAG:7200, 7300 series
- NTN:7200, 7300 series
- NACHI:7200, 7300 series
Interchangeability:
- Angular contact ball bearings in the 7200 and 7300 series can be interchanged among these brands, considering matching contact angles and dimensions.
2. Roller Bearings
Tapered Roller Bearings:
- SKF:30200, 30300, 32200 series
- NSK:HR32000, HR33000 series
- Timken:30200, 30300, 32200 series
- FAG:30200, 30300, 32200 series
- NTN:4T-30200, 4T-30300 series
- NACHI:30200, 30300, 32200 series
Interchangeability:
- Tapered roller bearings in the 30200, 30300, and 32200 series are typically interchangeable among brands, but it’s essential to verify the exact specifications.
Cylindrical Roller Bearings:
- SKF:NU, NJ, NUP series
- NSK:NU, NJ, NUP series
- Timken:NCF, NJ, NUP series
- FAG:NU, NJ, NUP series
- NTN:NU, NJ, NUP series
- NACHI:NU, NJ, NUP series
Interchangeability:
- Cylindrical roller bearings in the NU, NJ, and NUP series are generally interchangeable across these brands, with attention to internal clearances and dimensions.
3. Spherical Roller Bearings
Spherical Roller Bearings:
- SKF:22200, 22300, 23200 series
- NSK:22200, 22300, 23200 series
- Timken:22200, 22300, 23200 series
- FAG:22200, 22300, 23200 series
- NTN:22200, 22300, 23200 series
- NACHI:22200, 22300, 23200 series
Interchangeability:
- Spherical roller bearings in the 22200, 22300, and 23200 series are typically interchangeable among brands, provided the internal designations (e.g., cage type, clearance) are matched.
4. Thrust Bearings
Thrust Ball Bearings:
- SKF:51100, 51200 series
- NSK:51100, 51200 series
- Timken:51100, 51200 series
- FAG:51100, 51200 series
- NTN:51100, 51200 series
- NACHI:51100, 51200 series
Interchangeability:
- Thrust ball bearings in the 51100 and 51200 series are generally interchangeable across these brands, with similar dimensional specifications.
Spherical Roller Thrust Bearings:
- SKF:29300, 29400 series
- NSK:29300, 29400 series
- Timken:29300, 29400 series
- FAG:29300, 29400 series
- NTN:29300, 29400 series
- NACHI:29300, 29400 series
Interchangeability:
- Spherical roller thrust bearings in the 29300 and 29400 series can be interchanged among these brands, considering the exact dimensions and load ratings.
Interchanging bearings between different brands such as SKF, NSK, Timken, FAG, NTN, and NACHI is feasible due to standardized dimensions and specifications. However, it is crucial to verify the exact bearing type, series, and specifications, such as load ratings, internal clearances, and cage types, to ensure proper fit and performance.
Summary
At Loyal, we are committed to providing high-quality bearings that meet the rigorous demands of the mining and processing industry. By adhering to the principles and practices outlined in this guide, you can enhance the performance, reliability, and longevity of your equipment, ultimately leading to improved operational efficiency and reduced downtime.